The power of flexible manufacturing: Adapting production for efficiency and profitability
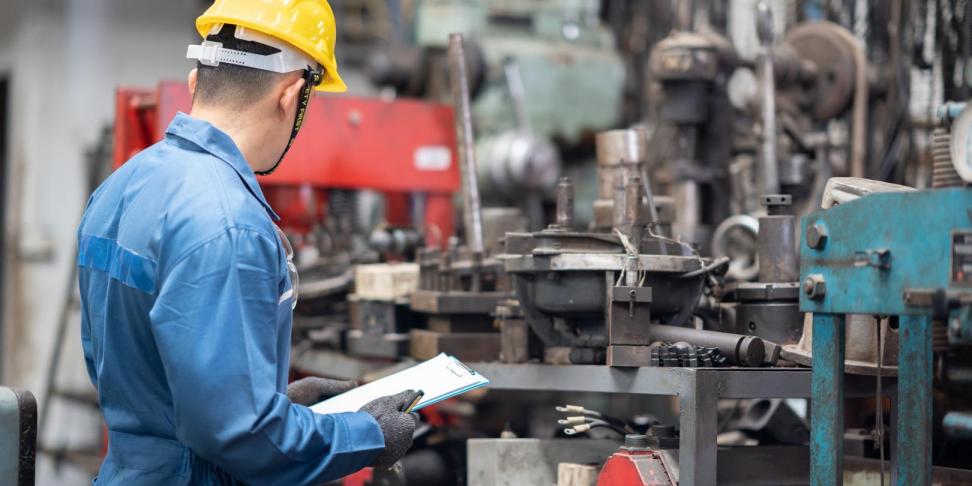
In today’s dynamic market, manufacturers face increasing demand for customization, shorter product life cycles, and fluctuating production volumes. Traditional production lines, designed for mass production of a single product, often struggle to keep up with these changes. This is where flexible manufacturing becomes a game-changer. By designing adaptable production lines, manufacturers can efficiently produce multiple product variations within the same family—maximizing equipment utilization, reducing downtime, and improving return on investment (ROI).
What is flexible manufacturing?
Flexible manufacturing is the ability to adapt production processes to accommodate different product variations without significant reconfiguration. Unlike rigid production lines that require separate setups for each product type, flexible systems use modular automation, smart tooling, and adaptable robotics to handle multiple variants.
For example, in metal casting operations, a flexible production line can process components of different sizes, weights, or geometries by automatically adjusting mold handling, pouring parameters, or cooling systems. Instead of creating a new setup for every variation, the same line can adapt to different parts within the same product family—reducing setup time and improving overall throughput.
Key components of a flexible production line
Implementing a flexible production system requires several key elements:
- Modular equipment – Machines that can easily be reconfigured or adjusted for different product specifications.
- Smart robotics & automation – Robots capable of handling multiple product types through interchangeable end-effectors.
- Advanced vision systems – Automated inspection and quality control systems that adapt to various product variations.
- AGVs & material handling solutions – Automated Guided Vehicles (AGVs) efficiently transport different components to the right stations.
- Smart data & industry 4.0 integration – Real-time data collection and predictive analytics optimize production scheduling and efficiency.
Benefits of flexible production
Improved equipment utilization & faster ROI
Traditional production lines often sit idle between product runs, leading to inefficiencies. Flexible manufacturing maximizes equipment use by allowing multiple product variations on the same line—reducing idle time and improving return on investment.
For more strategies on cost savings, read our blog on cost reduction in manufacturing.
Lower investment for low-volume production
High-volume production lines are cost-effective for large-scale manufacturing, but what about small batch or low-volume production? Flexible lines make it economically viable to produce smaller quantities of product variations without excessive setup costs—opening new market opportunities.
Faster changeovers & reduced downtime
Traditional production changeovers require significant retooling and adjustments, leading to downtime. Flexible systems use automated tool changers, smart sensors, and digital twin simulations to rapidly switch between product types—keeping production flowing.
Future-proofing manufacturing operations
Markets evolve, and product demands shift. Investing in flexibility ensures long-term adaptability, allowing manufacturers to quickly adjust production to meet new demands without costly overhauls.
Discover how smart manufacturing supports agile production strategies.
Examples of flexible manufacturing in action
Case 1: The Wheel Hub – Scalable and future-proof production
VDL Steelweld developed a flexible production line for The Wheel Hub, designed to grow with market demand. The solution enables production of various product types within a modular concept, allowing for phased automation and digital control from the start. The project integrates AGVs and vision technology for flexibility and precision. Read more
Case 2: Modular Housing – High-mix low-volume production
In the modular housing industry, VDL Steelweld delivered a flexible automation concept that supports the production of different panel types and layouts using a shared production line. By combining robotized processing with smart logistics and product tracking, the system offers a scalable approach for custom, sustainable housing modules. Read more
How to implement flexible production in your facility
- Assess current production capabilities and identify opportunities for flexibility.
- Invest in modular automation, robotics, and smart tooling.
- Implement real-time monitoring and predictive analytics for optimized scheduling.
- Train staff and refine operational workflows for seamless changeovers.
- Continuously improve through data-driven optimizations and Industry 4.0 integration.
Explore industrial automation for smarter production workflows.
The future is flexible
In an era of increasing customization and rapid market shifts, rigid production models are becoming obsolete. Flexible manufacturing allows companies to adapt, innovate, and maximize profitability without excessive investment in multiple production lines.
Looking to implement flexible automation? Contact VDL Steelweld to learn how our tailored solutions can future-proof your production.