5 proven strategies for cost reduction in manufacturing
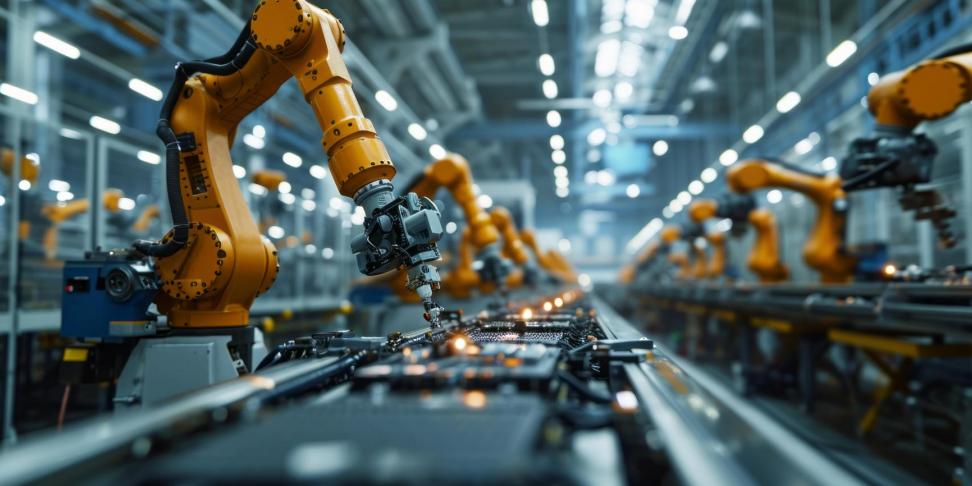
In today’s competitive market, manufacturers must continuously seek ways to reduce costs while maintaining quality and productivity. Rising material prices, labor costs, and energy expenses make cost control essential for long-term profitability. Fortunately, smart manufacturing strategies can streamline operations, minimize waste, and increase efficiency.
In this blog, we explore five proven strategies for cost reduction in manufacturing and how implementing these approaches can transform your production process.
1. Implement smart manufacturing for data-driven decisions
Smart manufacturing integrates technologies like real-time data collection, AI-driven analytics, and automated monitoring systems to enhance efficiency and reduce waste. By leveraging data, manufacturers can optimize production workflows, reduce material waste, and lower maintenance costs by predicting machine failures before they happen.
With virtual factory technologies, manufacturers can simulate production scenarios and test improvements before making costly physical changes. This minimizes trial-and-error in the real world and ensures every decision is based on data, leading to reduced waste and improved cost efficiency.
2. Automate repetitive and labor-intensive tasks
One of the most effective ways to reduce costs in manufacturing is through automation. Manual processes are often slow, error-prone, and labor-intensive. By integrating robotic automation and machine vision systems, companies can improve precision, reduce human errors, and lower operational costs.
Automation allows manufacturers to scale production efficiently. Robotic assembly lines and robot welding automation streamline processes by ensuring consistency in tasks like material handling, assembly, and quality control. These systems require less manual intervention and operate 24/7, reducing labor costs and increasing throughput.
Want to learn more? Read: The ROI of factory automation.
3. Optimize production with lean manufacturing principles
Lean manufacturing focuses on eliminating waste (time, materials, energy) while maximizing productivity. By implementing Just-in-Time (JIT) production, companies can reduce excess inventory and storage costs. Continuous improvement methods, such as Kaizen, help identify small but impactful process optimizations, while Value Stream Mapping (VSM) enables manufacturers to visualize and remove inefficiencies in production flows.
By integrating automated production lines and industrial machine vision, manufacturers can further streamline operations and maintain high-quality standards. Automation plays a key role in lean manufacturing by ensuring resources are used efficiently and production bottlenecks are minimized.
For a deeper comparison, check out: Lean manufacturing vs. Smart manufacturing: What’s the difference?.
4. Invest in predictive maintenance to prevent costly downtime
Unplanned downtime is one of the most expensive problems in manufacturing. Traditional maintenance strategies—fixing equipment only after it breaks—are reactive and costly. Predictive maintenance, on the other hand, uses real-time data and IoT sensors to detect potential issues before they lead to breakdowns.
By implementing predictive maintenance strategies, manufacturers can significantly reduce machine failures, extend equipment lifespan, and optimize maintenance schedules. This leads to lower repair costs and minimizes production disruptions. Companies using automated inspection systems benefit from early defect detection, improving overall production reliability.
5. Reduce energy consumption with smarter systems
Energy costs account for a significant portion of manufacturing expenses. Optimizing energy consumption is a key factor in reducing costs while also improving sustainability.
Manufacturers can lower energy expenses by automating energy-intensive processes, implementing AI-powered energy management systems, and using energy-efficient motors and machinery. CNC automation plays a vital role in this strategy, as it allows machines to operate only when necessary, reducing unnecessary power consumption.
Companies investing in energy efficiency also position themselves as sustainable manufacturers, which can be a competitive advantage in today’s market.
Cost reduction through smarter manufacturing
Manufacturers face increasing pressure to cut costs without sacrificing quality or efficiency. The best approach involves a combination of strategic automation, predictive analytics, and continuous process improvements. By integrating smart manufacturing and lean methodologies, businesses can significantly lower operational costs while maintaining high standards of production.
At VDL Steelweld, we specialize in customized automation and manufacturing solutions that help companies reduce waste, improve efficiency, and streamline their production processes.
Ready to cut costs and optimize your production?
Contact VDL Steelweld today and explore how automation, machine vision, and smart manufacturing can transform your factory operations.