Optimizing logistics in automated production lines
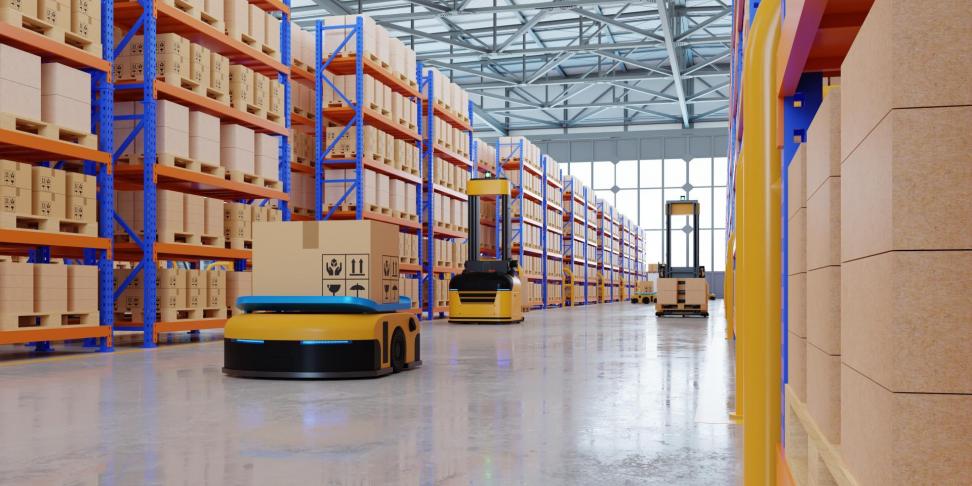
When automating a production line, the primary focus is often on improving efficiency, increasing throughput, and maintaining product quality. However, an often-overlooked factor in manufacturing costs is logistics—the movement, storage, and handling of materials within the production environment. Since logistics does not directly add value to the product itself, it is considered a secondary cost that should be minimized wherever possible.
By optimizing logistics in automated production lines, manufacturers can reduce waste, improve efficiency, and lower operational costs. This is one of the proven strategies for cost reduction in manufacturing, as eliminating secondary costs directly impacts overall profitability. This article explores how companies can achieve these benefits by rethinking material flows, optimizing packaging, and leveraging automation technologies.
The hidden costs of logistics in manufacturing
Every movement of raw materials, components, and finished products within a factory costs time, space, and labor. These hidden costs accumulate in ways that may not be immediately visible but significantly impact the bottom line. Some common inefficiencies include:
- Unnecessary handling: Materials being moved multiple times before reaching the production line.
- Suboptimal packaging: Packaging that slows down machine feeding or increases waste.
- Excessive transport: Small batch deliveries leading to higher internal transport costs.
- Workforce inefficiencies: Operators spending time moving materials instead of focusing on value-added tasks.
While logistics may not contribute directly to the product’s functionality or quality, it can impact overall production costs, cycle times, and even worker safety.
Optimizing logistics through smart packaging solutions
One effective way to reduce unnecessary logistics costs is by reconsidering how materials are packaged before they enter the production process. The goal is to ensure that materials arrive ready for processing, with minimal manual handling.
1. Packaging that supports automation
Traditional packaging is often designed with warehousing and transport in mind rather than the ease of automation. However, adapting packaging specifically for automated production processes can reduce the time and labor required to process materials.
Example:
Instead of supplying parts in bulk containers that require manual sorting, they can be pre-arranged in standardized trays or crates that are directly compatible with robotic arms or conveyors. This reduces the need for human intervention and speeds up material handling.
Other smart packaging solutions include:
- Using customized inserts that allow robots to pick items directly from a crate.
- Reducing protective packaging layers that slow down unpacking and feeding processes.
- Standardizing packaging dimensions to work seamlessly with robotic assembly lines.
2. Smart bulk loading to reduce transport costs
Delivering materials in larger, production-ready units can significantly reduce the number of internal transport movements and manual handling steps. By optimizing how and in what format materials arrive at the production line, manufacturers can improve flow efficiency and reduce secondary logistics costs.
Example:
Instead of delivering cast metal parts in small containers that require manual unloading and sorting, a manufacturer can switch to large, standardized steel pallets designed for direct feeding into robotic cells. These pallets are engineered for compatibility with automated lifting systems or conveyors, allowing entire batches to be positioned precisely where needed without human intervention. This approach minimizes transport movements, reduces operator involvement, and improves line continuity.
Integrating logistics with automation for maximum efficiency
For manufacturers already leveraging robotic assembly lines and automated inspection systems, integrating logistics with automation ensures that material handling is aligned with the rest of the production system. This requires data-driven material flow optimization and seamless communication between machines.
1. Smart warehousing and Just-in-Time (JIT) logistics
By linking warehouse systems with industrial automation, companies can reduce the amount of material stored on the factory floor. JIT logistics ensures that parts arrive only when needed, reducing clutter and improving efficiency.
For instance, smart storage systems can dynamically release materials based on real-time demand, reducing overstock and freeing up valuable factory space.
2. Automated material tracking & inventory management
When logistics and automation are connected through real-time tracking, manufacturers gain complete visibility into material flows. This allows for:
- Automated replenishment of production cells before materials run out.
- Immediate detection of bottlenecks in material supply.
- Reduced risk of waste and obsolescence by ensuring materials are used efficiently.
The business impact: Why optimizing logistics matters
Manufacturers focusing only on direct automation without considering logistics optimization may still experience inefficiencies. By addressing secondary costs, companies can unlock additional savings and improvements:
- Lower handling costs: Reduced labor required for material transport and preparation.
- Shorter cycle times: Materials arrive at the right place, in the right format, at the right time.
- Fewer production stoppages: Automation ensures a continuous and reliable supply of components.
- Improved workspace organization: Fewer material movements lead to safer and more structured production environments.
In combination with smart manufacturing and industrial automation, optimizing logistics creates a more efficient, cost-effective, and scalable production system.
Streamlining logistics for smarter manufacturing
While logistics may not add direct value to a product, its inefficiencies increase production costs in ways that often go unnoticed. By adopting optimized packaging strategies, AGVs for material transport, and data-driven logistics management, manufacturers can eliminate waste, reduce labor costs, and improve overall efficiency.
At VDL Steelweld, we specialize in developing fully integrated automation solutions. Our expertise ensures that manufacturers not only automate production but also optimize logistics for maximum cost savings.
Want to reduce logistics costs and enhance production efficiency? Contact VDL Steelweld today to explore how our factory automation solutions can help streamline your operations.