How manufacturing data drives efficiency and cost reduction
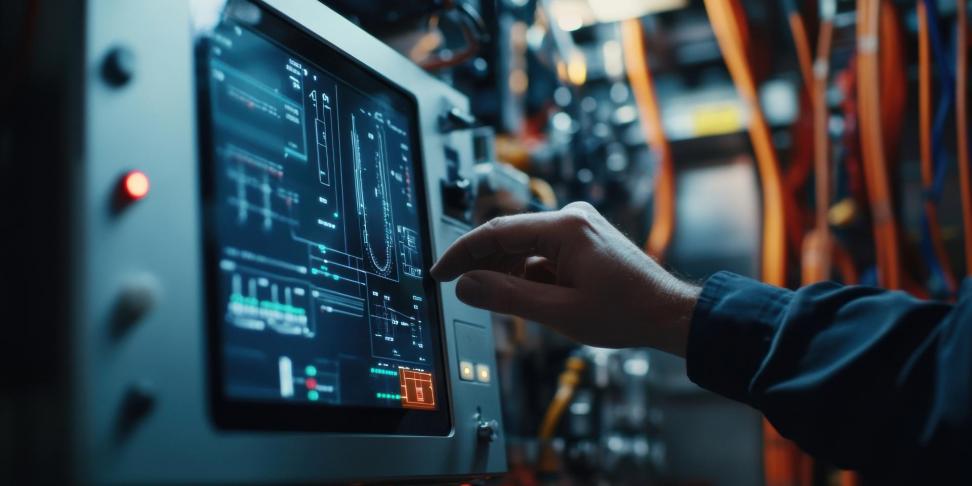
The manufacturing industry is undergoing a digital transformation, where data plays a crucial role in optimizing processes, reducing costs, and increasing efficiency. Companies that leverage real-time data gain better control over production lines, improve quality assurance, and make informed decisions to reduce downtime and material waste.
From live monitoring of production status to predictive maintenance and automated quality control, manufacturing data is shaping the factories of the future. But how exactly does data contribute to smarter production, and what technologies enable manufacturers to maximize its potential?
Real-time monitoring: Turning data into action
One of the biggest advantages of data-driven manufacturing is the ability to monitor production lines in real time. Instead of waiting for reports at the end of a shift, manufacturers can track machine performance, material usage, and quality output live.
- Live production tracking: Sensors and IoT-enabled devices provide real-time updates on machine status, material flow, and operational bottlenecks.
- Automated alerts: If a machine malfunctions or requires reloading, automated notifications inform operators before downtime occurs.
- Remote monitoring: Managers can access dashboards via cloud-based platforms or apps to make data-driven decisions from anywhere.
By integrating smart manufacturing solutions, companies gain full transparency over their production lines, helping them improve operational efficiency and reduce costs associated with unexpected machine failures.
Predictive maintenance: Reducing downtime and repair costs
Traditionally, manufacturers relied on scheduled maintenance or reactive repairs when a machine failed. However, predictive maintenance uses real-time data and AI-driven analytics to detect early signs of wear and prevent unexpected breakdowns.
How predictive maintenance works:
1. Sensors continuously collect machine data such as temperature, vibration, and pressure.
2. AI-driven analysis detects patterns that indicate potential failures.
3. Automatic alerts notify maintenance teams when intervention is needed—before breakdowns occur.
By implementing industrial automation with predictive maintenance, companies experience lower maintenance costs, fewer disruptions, and longer equipment lifespan, ultimately leading to significant cost savings.
Automated quality control: Preventing defects before they happen
Quality control is a key area where data enhances manufacturing processes. Instead of relying solely on manual inspections, automated inspection systems and machine vision technologies analyze products in real time, ensuring defects are identified immediately.
- Machine vision systems detect inconsistencies and defects at high speed.
- Automated feedback loops allow production lines to adjust settings when quality deviations are detected.
- Live reporting tools provide real-time insights on quality trends, allowing for continuous process improvement.
This data-driven approach to quality control reduces waste, rework, and product recalls, leading to better efficiency and cost reduction.
Data-driven decision making: Optimizing resources & production flow
With advanced data analytics, manufacturers can make strategic decisions that optimize resource allocation, workforce planning, and supply chain efficiency.
- Production data helps determine the most efficient batch sizes, reducing excess inventory and waste. In fact, data-driven process optimization is one of the key strategies for cost reduction in manufacturing.
- Energy consumption analysis identifies opportunities to cut operational costs.
- Supply chain data enables better forecasting, reducing material shortages and overstocking.
With automated production processes and real-time analytics, manufacturers gain the agility needed to stay competitive in dynamic markets.
The Future of data in manufacturing
As smart factories continue to evolve, data integration will become even more advanced. Future trends include:
- AI-driven process optimization: Self-learning systems that continuously adjust production parameters for peak efficiency.
- Digital twins: Virtual models of production lines that simulate performance before making physical changes.
- Blockchain for supply chain transparency: Ensuring real-time tracking of materials and reducing inefficiencies.
By embracing data-driven manufacturing, companies can unlock new levels of efficiency, cost reduction, and sustainability, ensuring they remain at the forefront of the industry. Investing in automation and data-driven processes not only improves efficiency but also delivers measurable financial returns, as discussed in our blog on The ROI of factory automation.
Turning data into competitive advantage
Manufacturers that invest in real-time data collection, predictive analytics, and automation position themselves for long-term success. Whether it’s reducing downtime with predictive maintenance, cutting waste with automated quality control, or optimizing workflows through live monitoring, data is the key to more efficient and cost-effective production.
Looking to integrate data-driven solutions into your manufacturing process? Explore our expertise in smart manufacturing and industrial automation to see how data can transform your production.