Scaling smart: How start-ups can implement automation in phases
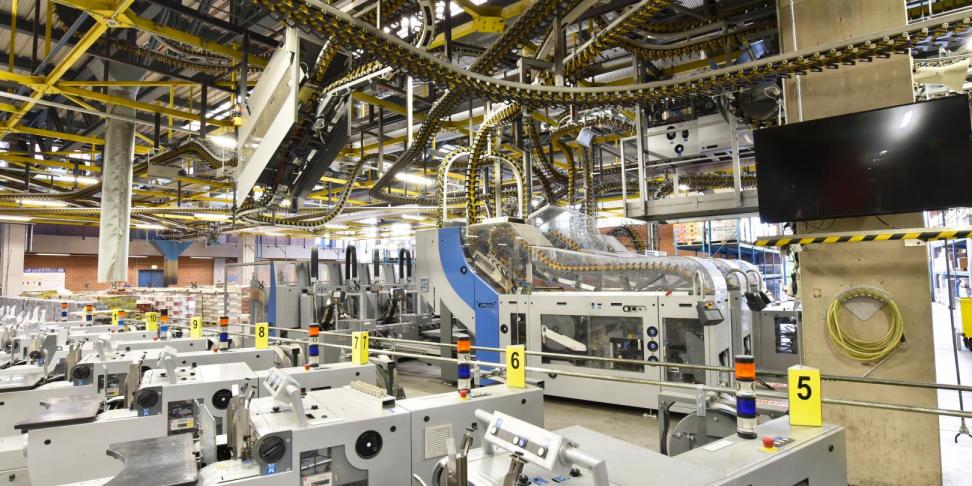
For many start-ups in the manufacturing sector, automation presents a major challenge. While established companies can invest heavily in fully automated production lines, start-ups often need a more flexible, scalable approach. Instead of implementing full-scale automation from day one, companies can benefit from a phased strategy that grows alongside their business.
At VDL Steelweld, we understand that automation must be tailored to a company’s maturity and production needs. By implementing automation in phases, start-ups can maintain agility, reduce initial investment costs, and build a scalable system that evolves over time.
Why start-ups need a phased approach to automation
Start-ups often face constraints that prevent them from investing in fully automated production lines right away. Limited capital, uncertain product demand, and the need for flexibility all influence automation decisions. By implementing automation in phases, companies can:
- Reduce upfront costs: Investing in automation step by step avoids large capital expenditures.
- Remain adaptable: Start-ups often need to pivot based on market demand. A flexible automation system allows for quick adjustments.
- Improve return on investment (ROI): Scaling automation in line with business growth ensures a more strategic allocation of resources.
- Mitigate risk: Implementing automation gradually allows companies to test solutions and optimize processes before committing to full-scale automation.
Phase 1: Semi-automation – Laying the foundation
The first step towards full automation involves semi-automated processes. Instead of relying entirely on manual labor or full automation, start-ups can introduce technology that supports operators in improving efficiency and reducing errors.
Key elements of semi-automation:
- Automated material handling to speed up logistics within the production process.
- Vision systems for quality control, reducing defects while still allowing human oversight.
- Basic robotics to handle repetitive but non-critical tasks.
- Operator guidance systems using light signals to guide manual part selection and reduce errors.
At this stage, automation does not replace human workers but enhances their productivity. This approach helps companies identify bottlenecks and determine which tasks benefit most from further automation.
Related article: How manufacturing data drives efficiency and cost reduction
Phase 2: Modular automation – scaling smart
Once production volumes increase, companies can begin to automate more critical processes. Modular automation allows businesses to scale specific parts of the production line without needing a complete system overhaul.
Examples of modular automation include:
- Automated assembly lines that integrate robotic systems for repetitive manufacturing tasks.
- CNC automation to improve precision in machining operations.
- Industrial automation solutions that optimize production efficiency while maintaining flexibility.
This phase enables companies to maintain manual operations in areas where flexibility is still required while automating processes that benefit from speed and consistency.
Phase 3: Full automation – building a smart factory
When a start-up reaches full-scale production, transitioning to fully automated systems becomes a viable and necessary step. Full automation includes robotic assembly lines, automated inspection systems, and smart manufacturing technologies that enable self-optimizing production processes.
At this stage, companies can:
- Implement real-time production monitoring to optimize efficiency.
- Use AGVs and AMRs for fully automated logistics within the facility.
- Integrate digital twins and virtual factory models to simulate and test production scenarios before making physical changes.
By investing in smart manufacturing solutions, businesses can enhance scalability, improve cost-efficiency, and remain competitive in global markets.
How VDL Steelweld Supports Start-ups in Automation
Many start-ups lack the infrastructure to install and operate an automated production line in their own facility. VDL Steelweld provides a unique solution: companies can operate their initial production at a VDL facility while they scale towards their own fully automated factory.
This flexible production model enables start-ups to:
- Begin production without major upfront investments in their own facility.
- Optimize their manufacturing processes before committing to a permanent location.
- Gradually transition to an independent, automated production line when the business is ready.
At VDL Steelweld, we specialize in helping companies scale automation in a way that aligns with their growth. Whether it’s semi-automation, modular upgrades, or full automation, we ensure that each step is optimized for efficiency and long-term success.
Related article: The ROI of factory automation
Start small, scale smart – the future of start-up automation
For start-ups in manufacturing, automation doesn’t have to be an all-or-nothing decision. By implementing a phased approach, companies can balance efficiency, flexibility, and investment in a way that supports sustainable growth.
Are you looking to scale your production with a smart automation strategy? Contact VDL Steelweld today to discuss how we can help build an automation roadmap tailored to your business needs.